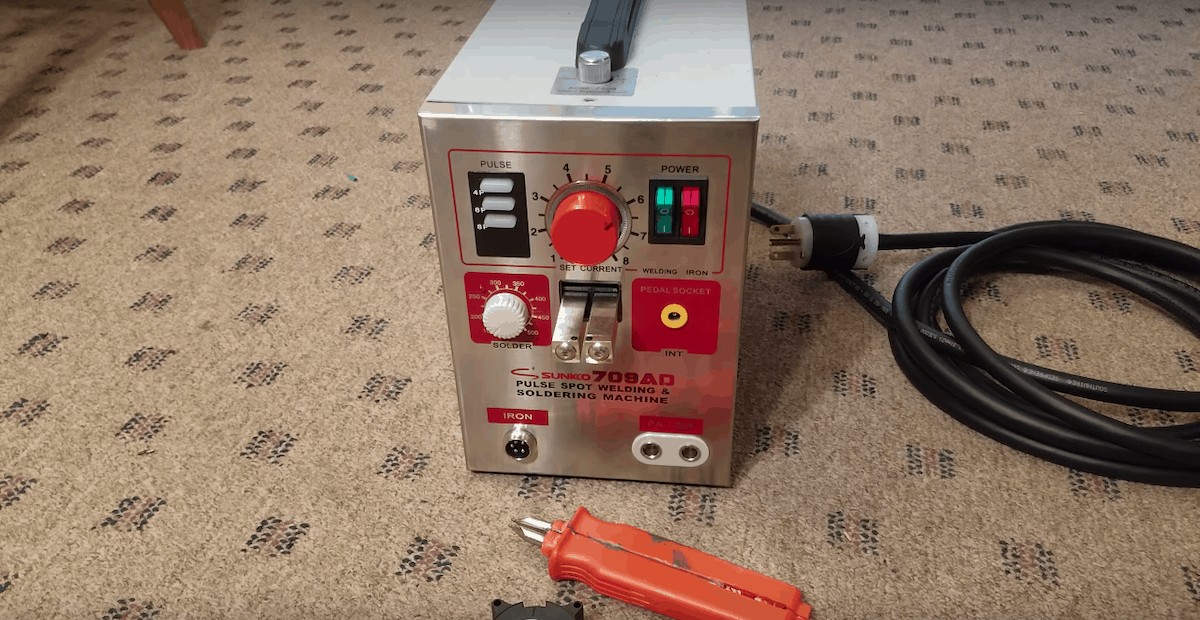
If you work with metals, there may come a time when you need to join two pieces of sheet metal together. How can you go about doing so? A spot welder could help you get the job done. Spot welders utilize the resistance welding process to apply heat and pressure to two sheets of metal.
Even if you only need a spot welder once in a blue moon, it could still be a useful tool to have on hand. Which spot welder should you consider buying? Below, we’ve included a list of the five best spot welders available today. We also added a spot welder buyer’s guide, so that you know what features to look for when making your purchase.
The Five Best Spot Welders Available Today
We tested numerous products and poured through hundreds of online reviews. After considerable research, we came up with a list of the five best spot welders available on the market today.
YaeTek Pulse Sparkle Spot Welder 200W
This miniature spot welder is ideal for fusing smaller metals like jewelry. This spot welder machine operates just like a full-sized welding machine, complete with a foot pedal. The device offers 200W of power, running on 110V 60HZ.
YaeTek says that this spot welder works with precious metals like gold, platinum, silver, and palladium. You could also possibly work with aluminum, tin, and other brass alloys. You’ll need to make sure that you use proper safety equipment with this device, as the resulting light is quite bright and could cause blindness.
What We Like
- Portable and easy to take with you
- Works with sensitive alloys like gold and platinum
- Comes with a foot pedal, so that there’s no new learning curve for those with experience using traditional welding machines
What We Didn’t Like
- YaeTek customer service is non-existent
- No warranty information
YaeCCC SUNKKO 719A Li-ON Battery Spot Welder Pen
This spot welder pen is made of low-resistance, oxygen-free copper material. You’ll find that this spot welder pen is quite stable. The pen is quite portable, making it easy for you to replace a weld at any soldering point.
One of the unique things about this product is that it runs on a lithium-ion battery. You’ll need to keep this battery charged for the device to work correctly. But compared to other spot welders, which require you to carry around a bulky power source, this piece of equipment is much more portable.
What We Like
- Incredibly portable
- Lithium-ion battery had a long lifespan
What We Didn’t Like
- Limited functionality – only works with 710 models
- Could be too small for traditional spot welder applications
Stark Professional Portable Spot Welder Machine
This portable spot welder machine from Stark features a single-phase design and a simple welding mechanism. It’s a useful tool for those who may not have much experience welding but still need the ability to do so.
This product also stands out because it comes with replacement tips. Instead of having to replace the entire spot welder pen, all you need to do is twist the tips off once they are ready to change and put the new ones in place. Stark made these welding tips with high-quality steel, and you should find that they are quite durable. But it’s nice knowing that you can replace them if necessary.
What We Like
- Single-phase design makes the product easy to use, even for beginners
- Replacement tips help extend the lifespan of the product
- An easy-to-use lever allows you to perform welding applications easily
What We Don’t Like
- You may need to play around with the handle tension to reduce sparks
Tooluxe RIDGE 10915L Professional 115V Electric Spot Welder
This spot welder from Tooluxe is another portable option that’s ideal for heavy-duty welding projects. Like the Stark product listed above, this tool features a single-phase design, making it easy to use wherever you go. Tooluxe designed this equipment for use with mild, galvanized, and stainless steel.
The device operates on 115V/60Hz of power. The throat depth is 180mm, which should make it large enough to work with sheet metal.
What We Like
- Easy to maneuver, allowing you to reach challenging welding areas
- We found that the welds were of high quality
What We Didn’t Like
- The trigger switch doesn’t automatically turn to the “Off” position
- Online reviews indicated poor customer service
Lenco Autobody Dual-Spot Welder
If you’re looking to invest in a high-quality spot welder that’s a bit more permanent, you’ll want to check out this product from Lenco. Whereas other spot welders come with clamps, this machine comes with two different separate arms that you can place anywhere.
Those looking to use this product should have considerable welding experience. Whereas other spot welders make it easy for both welding tips to line up, this is not the case with this product. You’ll need to be incredibly accurate when using this device. Otherwise, you risk ruining your metals.
What We Like
- A high-quality product that offers much more flexibility to users
- Comes with wheels, making it easy to tote the machine with you
What We Didn’t Like
- May be too advanced for inexperienced welders
- Quite expensive
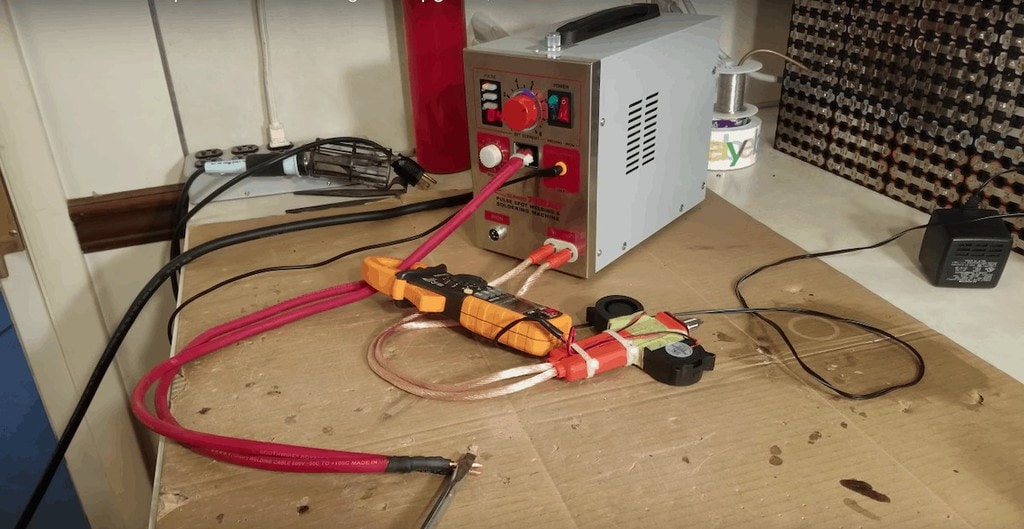
Everything You Need to Know About Spot Welding
Looking to add spot welding to your capabilities? Below, we’ve provided you with a guide to everything you need to know about spot welding.
What is Spot Welding and How Does it Work?
If you have two separate pieces of sheet metal, you may be looking to combine them so that you can work with a thicker piece. You can do so with spot welding. Spot welding is a form of resistance welding that forms two or more pieces of sheet metal together. You can often find spot welds in the automobile industry, where manufacturers use them to put pieces of the body together.
During the welding process, your machine will create thermoelectric heat. You will then apply this heat to the pieces of metal in areas known as “circular points.” Typically, spot weld machines will use copper alloy electrodes because of their ability to pass electrical currents. Depending on how much pressure you apply and the type of device that you use, your welds will be between 3 and 12.5 millimeters in diameter.
Metals That You Can Use When Spot Welding
One of the benefits of spot welding is that you can use it with a variety of different alloys and metal materials. Most welders will use spot welds when working on sheet metal or things such as wire mesh.
Welders tend to have the best luck when using steel to spot weld. That’s because steel has high electrical resistance and low thermal conductivity. Nickel, titanium, and stainless steel alloys all also tend to work well for spot welding.
You should avoid using metals with high carbon ratings, such as high carbon steel. Attempting to weld high carbon steel will likely result in a brittle material that is prone to fracturing or cracking.
Furthermore, you may find it too challenging to spot weld on materials that don’t conduct electricity very well. For instance, aluminum, zinc, and galvanized steel are not well-suited for spot welding because they need higher currents than the ones offered by spot welder equipment.
Lastly, you’ll want to consider the thickness of the metal before attempting your spot weld. In a perfect world, you would work with metals that were no thicker than three millimeters. Additionally, you want to make sure that the two metals that you’re combining have similar thickness levels. The ratio of thickness levels should never exceed 3:1. So, for instance, if one piece of sheet metal is three millimeters thick, the other should be no less than one millimeter thick.
The Benefits and Disadvantages of Spot Welding
There are a couple of pros and cons associated with spot welding. The most significant benefit of spot welding is that the welds are incredibly durable. The welds are reliable and are built to last.
Furthermore, spot welds are useful because you don’t need extra metal weld materials. Because spot welding relies on electrical currents that run through the attached electrodes, the only thing that you’re going to need is a power source. Thus, spot welds are a convenient option worth considering if the materials that you’re using allow you to do so.
You’ll also find that the spot weld process is quite quick. Because the machines are portable and you rely on nothing more than electricity, you can complete welds in a matter of seconds. Additionally, the spot weld process doesn’t require an extreme amount of heat, so you won’t burn the surrounding areas of your metal either.
Although you can use spot welds on an array of materials and products, it doesn’t work well for everything. You may find that your options for spot-welding are limited when working on a project.
Also, spot welds can be a useful tool for beginners because the machines are so easy to use. However, even beginners are going to need to practice to make sure that they are using the device correctly. If you don’t apply enough heat to the metal, it’s easy for the weld to fail. You’ll need to put a bit of time working with your tool to ensure your heat settings are correct before using the machine.
Lastly, one of the other pitfalls of spot welders is that they can be a bit challenging to maneuver. Unless you invest in a commercial-grade spot welder, you’ll find yourself limited by the position of the electrodes. If you’re working on a project with a weird shape, your spot weld tool may not work.
Terms Used with Spot Welding
There are primarily four terms used when discussing spot welding. Docking refers to the process of putting the two metal sheets between the electrodes. The act of welding occurs when you apply pressure to the two different plates. Forging occurs when you hold the two sheets of metal together between your electrodes. And “release” happens when you push the electrodes apart to separate the plates.
Frequently Asked Questions
What safety precautions should I take when spot-welding?
First and foremost, you’ll want to make sure that you read the safety instructions and operational guide on the piece of equipment that you purchase. The manufacturer will provide you with instructions on how to use the product. Following the manufacturer guidelines is the best way to ensure that you’re using the device correctly.
Remember that the electrodes on the machine will pass heat, no matter what’s between them. It’s entirely possible for you to burn yourself – or other materials, potentially starting a fire – when using a spot weld machine. Make sure that the electrodes are completely cooled before you set them down on a flammable surface. You should also wear gloves when completing the welds to maintain safety.
Additionally, spot weld machines will produce sparks, just like any other type of welding equipment. You’ll want to make sure that you’re wearing the proper eye and face equipment. Remember that you should never look directly into the light that a weld produces.
Can the electrodes get stuck?
It’s possible for the electrodes to become stuck when spot welding. This is known as electrode sticking and surface splash. This typically occurs because there is too much heat between the two materials that you’re attempting to conjoin.
Electrode sticking tends to occur when the electrodes are misaligned or when the force is too low. Additionally, a dirty work environment can contribute to electrode sticking. If your metal surface is dirty or contaminated, the electrodes can stick. The same is true if the electrodes are contaminated. Be sure to clean your equipment before attempting to spot weld.
Can you check weld quality?
Before you weld two metals together, we highly recommend that you test the alloys to ensure that the settings on your device are correct. You can do so through a process known as unbuttoning. Once you’ve welded the materials together, you should perform a destructive test with a forked chisel and hammer.
Doing so will allow you to test the strength of the weld. If the two metals come apart quickly during this process, you’ll need to go back to the drawing board. You’ll also want to check for a hole in one of the two metals. If there is a hole in one of the metals, it means that the weld held. This process is known as “unbuttoning.”
Can you use single-side resistance spot welding?
As we’ve mentioned, one of the limitations of spot weld tools is that they may not reach all areas. However, you cannot use single-side resistance spot welding as a substitute for any sort of structural welding. If you’re working on a body shell or a large piece of metal, you’ll need to use a double-sided technique.
However, if you’re looking to make cosmetic touch-ups to a piece of metal, it’s possible that single-sided resistance spot welding could work. However, these scenarios are rare. Try always to use double-sided spot welds when possible.
Are there any other precautions to take when welding?
You may want to consider adding corrosion protection to your two metals before welding them together. This can include things like bonders and sealers, which would act as sound deadeners. It would also include things like primers and finishing paint coats. You can weld through these materials without a problem.
However, before you do so, you’ll want to perform a test to make sure that it’s safe. You should read the labels on these materials before welding. These materials could be highly flammable. But, if it’s safe to do so, we recommend that you weld thorough any corrosion protection that exists between your two metal materials.
Final Thoughts
There are numerous different types of spot welders available on the market today. We feel that the best spot welder for most people is the machine from Stark. We liked the fact that this tool has a single-phase design and a clamp system, making it quite easy for you to weld pieces of metal together.
We also liked how portable this equipment was. Lastly, we were fans of the fact that we could replace the tips on the spot welder, which increased the durability of the product. For the average welder, this product should prove more than worthwhile.
If you have experience welding and are looking for a device that will provide you with a bit more flexibility, be sure to check out the machine from Lenco. Although this device is expensive, it’s a machine that experienced welders will want to have in their arsenal.
No matter your experience level, you should be able to find a spot welder that best suits your needs. We hope that our spot welders buyer’s guide proved useful in providing you with the information you need to make an informed purchasing decision. What will you purchase? Tell us in the comments.
The welding tips can’t be steel. They must be pure copper. That it was stated that the tips for the spot welder were “high quality steel” makes me suspicious that they didn’t actually have the welder, and that they don’t understand how spot welders work.
That in turn makes me suspicious of their entire review process.